
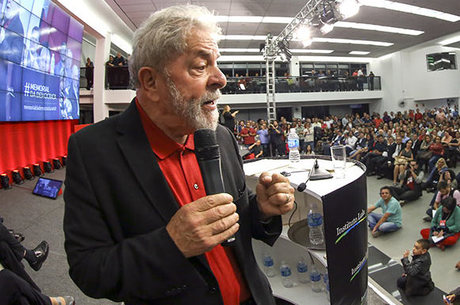
Maximizing the P-F Interval, which can be days, weeks, or months depending on Inspection Methodology! The P-F Curve and the P-F Interval
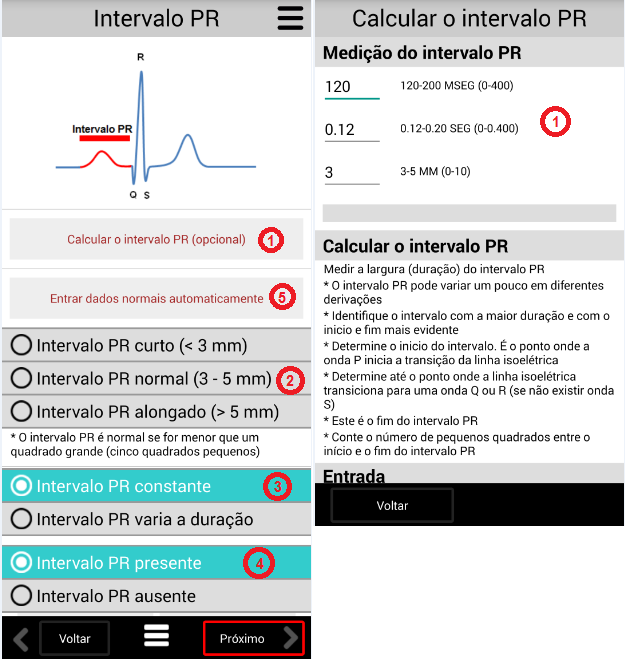
However, if the consequence of failure is not negligible, for example when production loss or costs of repair are high, then it will almost always be worth the effort to detect the failure “process” as early as possible before the failure, so that we may take whatever corrective action required to either avoid the failure, if possible, or reduce its consequence.įigure 3. If the consequence of failure is small or negligible, we may choose to do nothing, especially if doing something costs more or has more negative consequences than doing nothing. The good news is that when these kinds of failure causes take significant amounts of time to actually create loss of function, we can often choose from alternative courses of action. Rather, our job is to maintain physical assets in such a way that we can avoid the consequence of failure, whatever its cause.Ī little wear, deterioration or contamination is not necessarily a problem a lot of wear, deterioration or contamination is almost always a problem. For example, belts and bearings can fail due to normal wear alone, such failure can’t actually be avoided. Sometimes failures are due to normal causes, and cannot be avoided.
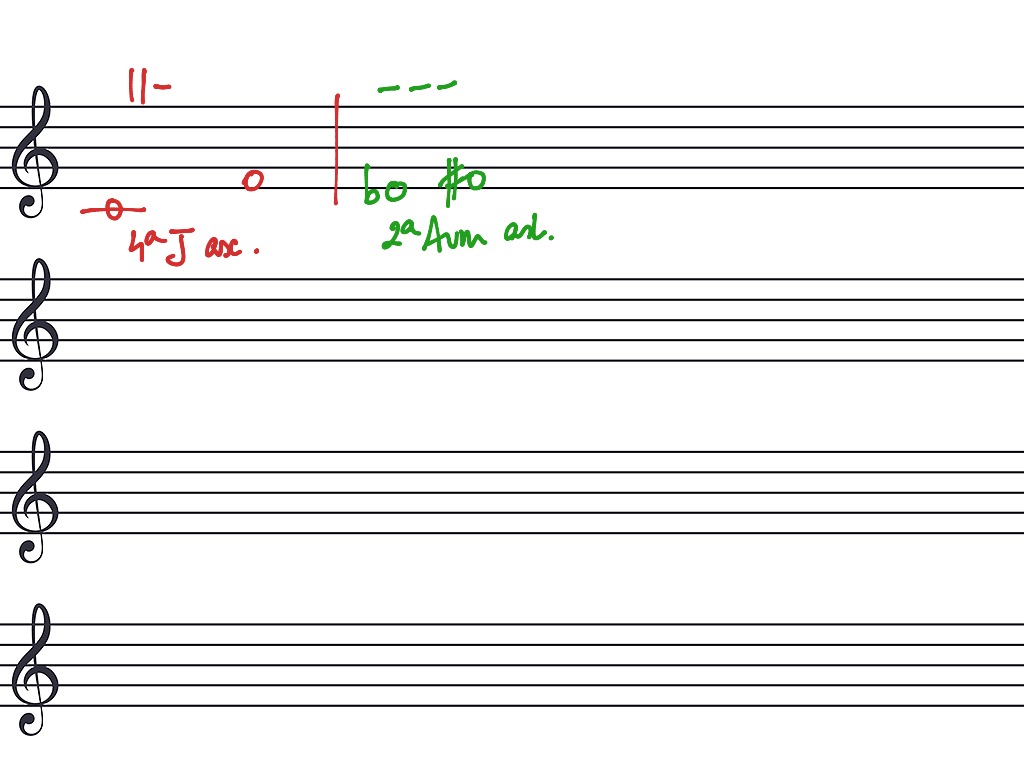
Our job is not to avoid failure altogether. Remember, our job in maintenance is not to “fix it when it fails”. We can often rely on this time interval to detect or correct processes leading to failure, and if not avoid failure altogether, at least be able to reduce or avoid the consequences of failure. Better yet, that time interval preceding failure is often long enough to be useful. Though failure may inevitably occur from any or all of them, many of them generally take time to develop to a level or degree that actually causes the failure. fortunately do not lead to failure immediately, or all at once. Common causes leading to failure like wear, stretch, deterioration, misalignment, contamination, etc. It’s really the causes of failure that take time, of course. We can say that (most) failures take time, and for that we can be thankful. There is a sense in which failure is a process, not an event. The P-F Curve (Figure 1) is a common way to represent the behaviour of an asset (pump, motor), or asset component (belt, bearing) before actual functional failure has occurred. Marshall Institute a maintenance professional, unless you have been sleeping under a rock these last ten or so years, you will have at least heard of the “P-F Curve”, even if you don’t understand it, or use it to your advantage.
